Industry Overview
Mixing is vital for consistent pharmaceutical products. Selecting suitable equipment depends on substance thickness, size, and chemical composition. Testing ensures fast and efficient production of uniform products
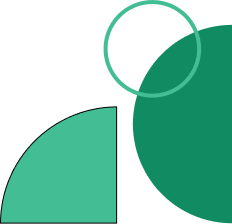
Challenges Addressed
In pharmaceutical production, blending ensures ingredient uniformity. Operations like crystallization, fermentation, and emulsification are crucial for high-quality products.
Crystallization is the quality defining unit operation. For active pharmaceutical ingredients, mixing can impact the PSD, impurity profile and polymorphic form. For intermediates, mixing may affect the batch cycle time due to longer filtration and drying times. Knowledge-based Mixing scale-up to reproduce lab scale mixing at production scale ensures right first-time plant process validation and batch-to-batch consistency.
Scale-Up
Pharmaceutical chemistry scale-up is challenging for fast and heterogeneous reactions and when accompanied with undesired side reactions, an improper mixing at plant scale can result in batch failures, increased downstream processing cost and longer batch cycle times (reduced productivity). An in-depth evaluation of mixing parameters is essential to ensure the achievement of lab yield and impurity profile at plant scale.
Fermentation in the pharmaceutical industry is used to cultivate microorganisms for antibiotics, therapeutic proteins, enzymes and insulin. Scalability of such process is highly challenging as many parameters such as pH, dissolved oxygen concentration, dispersion of air bubbles, and shear rate are critical for desired microorganism culture growth and life.
Solid dissolution is an important unit operation during solid-liquid mixing in the pharmaceutical industry. Incomplete dissolution can result in sub-potent/ low quality batches resulting in batch failure. Mixing equipment and mass transfer rates dictate the solid suspension level and the time required for dissolution. An extended dissolution time may increase the potential of microbial contamination.
Uniform blending in pharmaceuticals formulation relies on probes tracking ingredient mixing across blenders, optimizing blend spots by powder order/quantity. Mixing is essential for the preparation of liquid formulations, such as syrups, suspensions, and parenteral solutions and for topical pharmaceutical formulations, including ointments and creams. Proper mixing ensures the uniform distribution of APIs and excipients in liquid pharmaceutical products and semi-solid dosage forms improving dosing accuracy.
Emulsions aid in delivering active ingredients effectively by dispersing small liquid droplets, crucial for optimizing drug delivery efficacy. The mixing impacts droplet size distribution, average drop size, stability and rheological properties of finished formulation. Mixing parameters such as agitator type, pumping capacity and shear rate play crucial role in the scale-up of emulsification process.
Use Cases
Unlock the power of process optimization! Dive into our use-case library to explore real-world examples of how companies across industries leverage our solutions. Discover how we've worked on challenges like yours and empowered our customers to achieve their goals.
Why Tridiagonal Software

A skilled blend of chemical engineers with post-grad and PhD qualifications

500+ man-years serving Fortune 500 Pharma clients worldwide.

For optimizing and analyzing process conditions.


Incorporating best practices and methods to create and deliver value for customers.

Our Products
Tridiagonal Software provides industry-agnostic solutions that unlock the full potential of your processes. Our software solutions empower users with deep insights, enabling confident decision-making and optimized process performance.
- Remove roadblocks that restrict process optimization.
- Gain a deeper understanding of assets and process.
- Make decisions with confidence while optimizing process performance.